Introduction
In the world of motorsports and high-performance automotive engineering, the forged steel crankshaft is a key component that significantly influences engine durability, strength, and overall performance. It transforms the linear motion of the pistons into rotational motion, driving the vehicle forward. Due to its exceptional strength and resistance to wear, it is the preferred choice for racing engines and heavy-duty applications.
Why Choose Forged Steel Crankshafts?
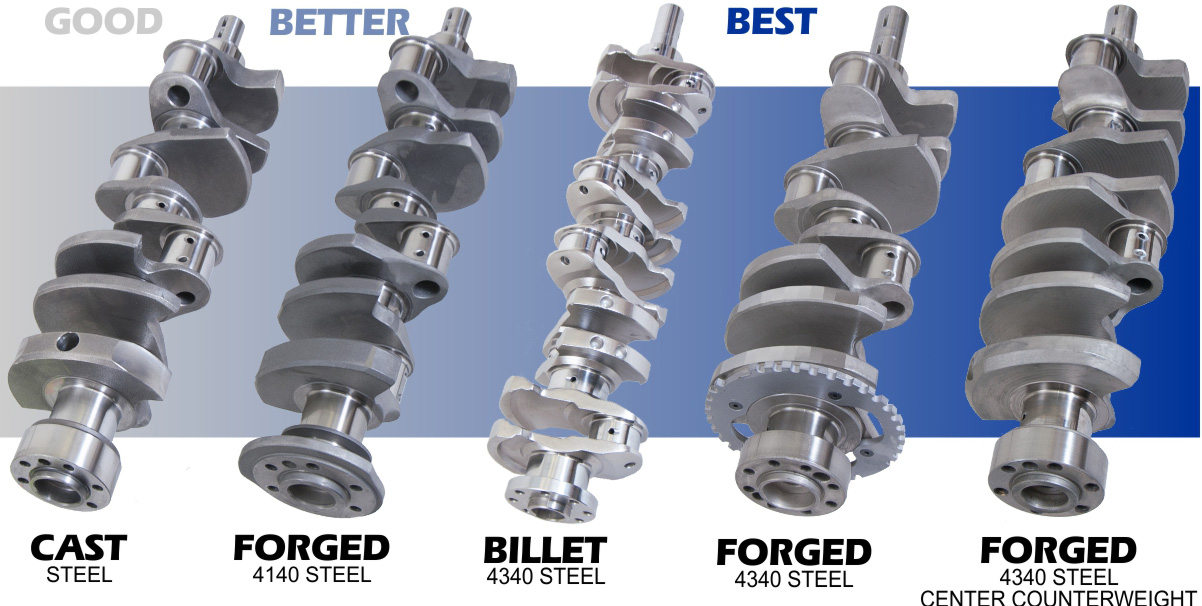
Superior Strength and Durability
Forged steel crankshafts are known for their remarkable strength compared to cast or billet crankshafts. This strength comes from the forging process, where high-pressure compression refines the steel’s grain structure, aligning it for maximum durability. Materials like 4340 steel are commonly used, offering tensile strengths between 140,000 to 165,000 psi, making them ideal for engines that endure extreme loads.
Enhanced Fatigue Resistance
One of the key advantages of forged crankshafts is their resistance to fatigue and wear. These crankshafts endure high RPMs, intense vibrations, and other stresses common in racing environments without suffering from cracks or deformation. Processes like heat treatment and nitriding are employed to harden the crankshaft surface and extend its lifespan.
Improved Grain Structure
The forging process gives crankshafts an improved grain structure, which enhances the overall mechanical properties of the component. This results in higher impact resistance, better load-bearing capacity, and reduced risk of failure during high-performance use.
Performance at High RPMs
Forged crankshafts provide better balancing capabilities, which is essential for engines that operate at high RPMs. By reducing vibrations and improving power transmission efficiency, forged crankshafts enhance the reliability of the engine, especially during competitive racing.
Manufacturing Process of Forged Crankshafts
The manufacturing process of a forged crankshaft is detailed and precise, involving multiple stages:
Material Selection
High-performance alloys such as 4340 or 5140 steel are typically used. These materials are chosen for their high tensile strength and ability to withstand fatigue.
Forging and Heat Treatment
After forging, the crankshaft undergoes heat treatment processes like quenching and tempering, which improve its hardness and reduce brittleness. Nitriding is often used to increase surface hardness, further enhancing the crankshaft's fatigue life.
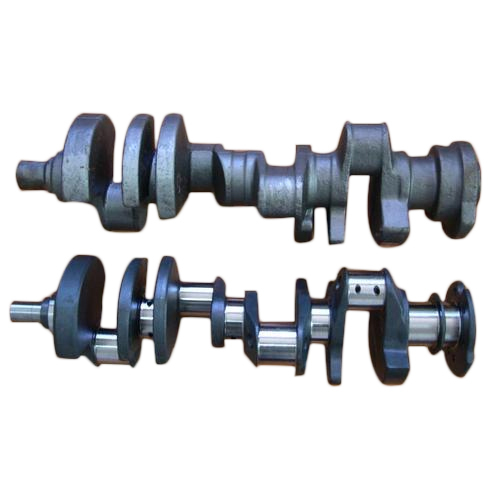
Precision Machining
The final steps include machining for precise dimensions and micro-polishing to eliminate surface imperfections. This ensures smooth operation and reduces friction between the crankshaft and bearings.
Applications in Motorsports and Beyond
Forged steel crankshafts are indispensable in high-performance racing engines, from NASCAR to endurance racing. They are also used in industrial applications, where high-load capacity and durability are critical. Forged crankshafts can handle higher horsepower and extreme conditions better than their cast counterparts, making them essential for engines producing over 750 horsepower.
Conclusion
For those looking to build or upgrade high-performance engines, investing in a forged steel crankshaft ensures maximum durability, reliability, and performance. Whether it’s for motorsports or heavy-duty applications, the strength, fatigue resistance, and precision offered by forged crankshafts are unparalleled.